Screw Machined Parts and Products
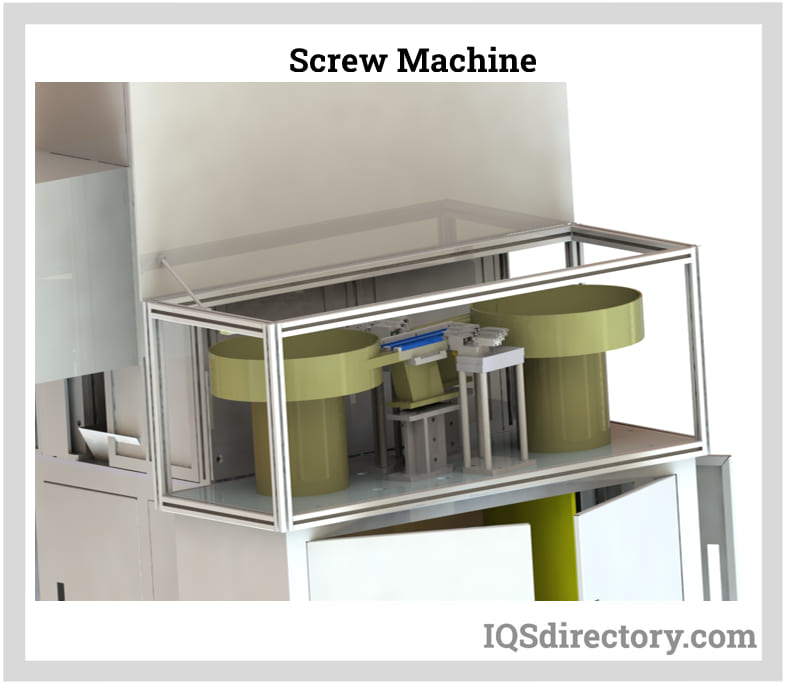
Screw machined parts are complex pieces that are typically cylindrical and threaded and a screw machined product is a family of automatic lathes for small to medium-sized components...
Please fill out the following form to submit a Request for Quote to any of the following companies listed on
This article contains everything you will need to know about precision turned products and their use.
You will learn:
Precision turned components are manufactured with meticulous attention to achieve very tight tolerances through the use of Swiss and CNC turning techniques. These precision turning operations encompass a range of procedures, including facing, chamfering, threading, tapping, drilling, and knurling. Each technique is employed to modify the workpiece to meet specific requirements. The turning process involves rotating the workpiece while a cutting tool meticulously removes material to achieve the precise shape and dimensions needed for the final product.
Precision turning produces components with exceptional accuracy and tight tolerances, resulting in high-performance parts. These components significantly improve the functionality of machinery and equipment, and are crucial for executing complex processes. Their widespread adoption is attributed to their durability and efficiency, which contribute to extended equipment lifespan, reduced waste, and energy savings.
Selecting the appropriate manufacturer for precision turned components is essential for ensuring the success of the final part and its assembly. Reputable manufacturers are often certified by organizations such as the International Organization for Standardization (ISO), Europäische Norm (EN), and the American National Standards Institute (ANSI). These certifications are crucial as they ensure adherence to rigorous quality standards in manufacturing processes.
Precision turned parts are produced using various machines, including Computer Numerical Control (CNC) machines, Swiss screw machines, and CNC automatic lathes. CNC machines offer the benefit of executing multiple operations in a single cycle. Meanwhile, CNC lathes and Swiss screw machines are particularly adept at creating highly complex and detailed components.
Precision turned parts can be manufactured from a range of metals, such as stainless steel, carbon steel, brass, titanium, silver, gold, and various alloys. These materials are selected for their suitability in achieving high precision, versatility, and efficiency in the production process. The precision turning methods are favored for their ability to deliver accurate results quickly, thereby minimizing cycle times.
Swiss screw machining was initially developed to produce watch components with precision that handcrafting could not achieve, and it has been employed for decades in the production of precision turned parts. The integration of CNC machining with Swiss screw technology has resulted in the creation of high-quality components that satisfy the requirements of various industries.
Swiss screw machines come in various models, but they all share fundamental components such as the workpiece bar stock holder, chuck collet, guide bushing, and headstock. These elements work together to precisely cut and shape the workpiece according to the desired specifications of the part.
To achieve precise cuts on the workpiece bar stock, it must be firmly secured to avoid vibrations or movement during rotation. Properly holding the workpiece helps safeguard the spindle and cutting tools while maintaining cutting accuracy. There are two main types of bar feeder holders—hydrodynamic and hydrostatic—each offering a different method for securing the workpiece.
Hydrodynamic part holders, also known as breech-loading bar feeders, secure the workpiece bar stock within an oil-immersed liner, which helps to automatically center the bar. This method minimizes noise and vibrations during the process. In a Swiss screw machine, bars are fed individually, and the feed tubes need to be replaced when the diameter of the bar stock changes.
Hydrostatic bar feeders utilize guide channels or bushings that clamp around the bar stock, with an oil film providing support as the bar moves towards the chuck collet and guide bushing. Unlike hydrodynamic feeders, hydrostatic bar feeders can accommodate bar stock lengths of up to 24 feet (7.315 meters) and are designed as magazine-type loaders, allowing for the processing of various diameters of bar stock without the need for adjustments or modifications.
The bar stock feeder advances the workpiece into the chucking collet, which grips the workpiece securely using force. The chucking collet consists of a three-jaw chuck, a hydraulic cylinder, and a drawtube. This compact cylindrical component features the hydraulic cylinder connected to the rear end of the spindle, with the chuck positioned at the front. The drawtube generates the clamping force that links the hydraulic cylinder and chuck to the spindle, ensuring a firm hold on the workpiece.
The selection of a chucking collet is based on the spindle nose configuration, with international standards defining the mounting interface dimensions. Common spindle nose configurations include A2-6, A2-8, and 140 mm. Additionally, the size of the chucking collet is influenced by the drawtube's bore size. After establishing these initial criteria, more detailed parameters are considered to select the most suitable chucking collet for a Swiss screw machine.
The guide bushing is a distinctive component of Swiss screw machines, setting them apart from conventional lathes. Its primary function is to support the workpiece during machining, preventing deflection during the cutting process. Guide bushings enable cutting tools to achieve the desired depth of cut in a single pass, rather than requiring multiple passes. This feature is crucial for ensuring accurate and precise cuts in Swiss screw machines.
Guide bushings come in three main types: rotary, fixed, and precision. Each type serves a specific purpose based on the required level of precision and the size of the workpiece. Rotary guide bushings rotate with the workpiece and are suitable for larger, broader parts. Fixed guide bushings stay stationary while the bar stock rotates, making them ideal for precision components with tighter tolerances. Precision guide bushings, akin to those used in early Swiss screw machines, are designed for producing small, detailed, and complex parts.
The headstock is a distinctive feature of Swiss screw machines, enabling the workpiece bar stock to be aligned along the Z axis. Unlike traditional lathes, where the workpiece moves towards the cutting tool, the headstock in a Swiss screw machine moves towards the workpiece, which is held in place by the collet. This design minimizes lateral forces and ensures exceptionally accurate and precise cuts.
With the guide bushing and chucking collet securing the workpiece, the headstock positions the cutting tools and workpiece close to the guide bushing, typically within a few millimeters or inches. This setup allows for a variety of cutting processes to be performed, enabling any part of the workpiece to be shaped, cut, and formed as needed.
The spindle of a Swiss screw machine supports the tools used to shape and form the workpiece bar stock. Among the various spindle types, the three most prevalent are direct drive, belt drive, and integrated spindles, each with distinct configurations and drive mechanisms. Belt-driven spindles, for instance, feature an adjustable pulley system that allows them to achieve high torque and speeds up to 8,000 rpm.
A direct drive spindle features the motor directly connected to the spindle shaft, enabling speeds of up to 12,000 rpm. This type of spindle is known for its exceptional accuracy and is ideal for high-speed applications. Direct drive spindles are favored for their low noise levels, in contrast to belt-driven spindles, which can suffer from issues such as belt slippage.
Spindles come in various types, including gear-driven, air turbine, electric motor, woodworking, cartridge, and high-frequency models. The choice of spindle type and design for a Swiss screw machine depends on the specific requirements and intended use of the machine.
To address the limitations of using a single spindle for machining, the multi-spindle design was introduced, allowing multiple tools to simultaneously work on a workpiece. This innovation has enabled Swiss screw machines to be effectively utilized in high-volume production environments.
CNC machining has gained widespread adoption due to its reliance on preprogrammed computer codes that guide the machine's operations. These codes, entered into the CNC machine, control the movements, cuts, angles, and other parameters of the tools and machinery involved in the process.
CNC machining reduces the need for direct operator involvement by using programmed commands to control the machine. The programming specifies the cuts to be made, their depths, and allows the machine to perform multiple operations in a single cycle.
CNC machines are programmed using G-code, a language generated by computer software. This software allows for simulation of the program to detect and correct errors before actual machining begins, preventing design flaws that could result in defective products. The software also manages various aspects of CNC machine operation, including tool positioning, process speed, and cycle times.
Computer-Aided Design (CAD) files are converted into command codes for CNC machines to execute. An initial trial run is performed to check for any coding errors. N-codes are utilized to label specific lines or blocks of G-code, helping programmers organize and manage the code more effectively.
CNC machines use either open loop or closed loop systems for position control. In an open loop system, there is no feedback during machining; tools stop based on predetermined commands after completing a cut. This type of system is more cost-effective and does not require encoders or controllers. It is suitable for applications where minimal force is needed, helping to reduce overall costs.
In contrast to an open loop system, a closed loop system incorporates sensors that provide real-time data on the position of moving components. The controller uses this data to stop movement when the desired position is achieved. Closed loop systems can vary in design but ensure precise positioning of both the workpiece and tools along the X and Y axes. The movements within the system are guided by the G-codes.
Today, Swiss screw machines are often integrated with CNC technology to enhance and refine the precision of the machining process. Both types of machines utilize cutting tools mounted on a tool holder or spindle to achieve the most accurate cuts and tolerances. CNC Swiss screw machines employ turning tools to reduce the diameter of the workpiece bar stock, either by rotating the workpiece or moving the cutting tool.
While turning tools vary in design, they all share a fundamental structure comprising several key elements: the holder, clamp, screw, insert, and seat. Inserts are specifically designed to ensure precision and efficient material removal. Each insert type is classified according to ANSI standards, which specify its shape, clearance, tolerance, type, size, thickness, and nose radius.
ANSI Insert Designations | |||||||
---|---|---|---|---|---|---|---|
C | N | M | G | - | 4 | 3 | 2 |
1 | 2 | 3 | 4 | 5 | 6 | 7 | |
Shape | Clearance | Tolerance | Type | I.C. Size | Thickness | Nose Radius |
Inserts are typically composed of materials such as carbide, ceramic, cermet, or diamonds, with ceramic, cermet, and diamond inserts being used for more demanding tasks. To enhance performance, inserts are often coated to enable faster cutting and increased durability. Each insert is supported by a seat, which is placed between the insert and its mounting location. The insert and seat are secured to the tool holder, which ensures stability by preventing deflection and vibrations. While the tool holders are made from heavy-duty forged steel, the bodies of turning tools are not precision-engineered. However, inserts are carefully engineered and fine-tuned to achieve high accuracy, tight tolerances, and effective coolant delivery to the cutting edge.
Chamfering Tool – Chamfering tools bevel the end of a workpiece and have an angled cutting surface to remove sharp edges on parts. The process is used to make parts stronger and give them a better appearance.
Knurling Tool – The knurling tool is used to create a pattern of straight, angled, or crossed lines on a cylindrical workpiece and has a shoulder and toothed wheels or knurls.
Contemporary manufacturing demands that assembly parts be machined to exact specifications, meet the highest quality standards, and perform reliably. Precision turning depends on the accuracy of Swiss screw machines and CNC machines, which are designed to produce components with the precision, accuracy, and tolerances required by modern industry standards.
Precision turned products encompass a vast array of components utilized across various industries. As precision turning is critical for manufacturing key parts for complex machinery, many of these components are produced in large quantities to satisfy demand. These parts are crafted from raw materials using Swiss screw machines or CNC machining, where the workpieces are rotated and meticulously shaped to achieve the highest accuracy and consistency.
Precision fittings serve as connectors to join or secure components, and are produced to exact dimensions to guarantee the strength of the connection. These fittings enable elements to align properly and come in various shapes, sizes, and configurations. Achieving the correct dimensional tolerances through precision turning is crucial, as even minor errors can result in product or part failure.
Bushings are a common type of part produced in high volumes through precision turning. They are designed to reduce friction between surfaces and maintain alignment, often referred to as plain bearings. Bushings support rotating and sliding shafts and are made from soft metals with precise dimensions and smooth surfaces to ensure optimal performance. Like fittings, bushings must be machined with exceptional accuracy due to their material properties and the demanding applications they serve.
Rings are manufactured using precision turning to meet the stringent requirements of their various applications. Similar to bushings, rings need to have smooth surfaces and exact dimensions to fit their intended use. They are commonly employed for sealing and bearing applications in industries such as food processing, medical devices, mining, and power generation. Given the critical nature of these applications and the materials involved, rings must adhere to the most demanding specifications and complex geometries.
Flanges are circular components used to connect and align pipes, featuring bolt holes that must be evenly spaced around their perimeter. Precision turning ensures that flanges are shaped to exact dimensions and that the bolt holes are accurately spaced, all within a single cycle of a Swiss screw machine or CNC machine. Flanges are available in various sizes and configurations to suit different applications and are constructed from durable metals designed to withstand significant stress and pressure.
Pins and dowels are versatile components used in precision assemblies to locate and secure parts, as well as to guide adjacent components. These small cylindrical rods are machined in various sizes to fit into holes that connect different surfaces and parts. Unlike threaded fasteners, pins and dowels can be inserted and removed multiple times, making them ideal for aligning parts. Available in a wide range of sizes and styles, each type of pin or dowel requires precise dimensional tolerances to ensure proper function.
The strength, thickness, and durability of pins and dowels make them ideal for aligning joints across various materials. They can serve as replacements for screws with stripped threads and are used to secure hanging items. Pins and dowels come in several forms, including standard, oversized, grooved, pull, and spiral grooved types, and are machined from a range of metals and plastics.
Spacers are among the most straightforward types of precision turned parts. They are designed to fill gaps and must have precise diameters and lengths to ensure they do not obstruct the functioning of an application. In addition to adjusting the space between surfaces, spacers are used to reduce vibrations and provide resistance to corrosion. Their primary role is to mitigate vibrations, which can otherwise compromise the quality of products and equipment.
Pulleys are designed to alter the direction of applied force and decrease the effort needed to lift a load. They are integral to various industrial applications and come in multiple forms tailored to meet specific requirements. Often, pulleys are used in combination to further minimize the force required and optimize energy and motion efficiency.
Precision turning is essential for manufacturing a variety of pulleys due to its high accuracy, as pulleys must meet specific ratios to function effectively. The machining process for pulleys varies depending on their shape and type, with some featuring deep grooves and others having gripping teeth. Regardless of the design, pulleys are crucial components in many applications and are produced with meticulous precision to ensure optimal performance.
The integration of precision turned parts into industrial manufacturing has significantly improved the quality, performance, and durability of products and assemblies. The tight tolerances and high accuracy achieved through precision turning have enabled manufacturers to ensure greater product longevity. This enhancement in product quality has not only attracted more buyers but also boosted profitability.
The success of precision turned parts hinges on their exceptional accuracy and the capability to achieve tolerances within just a few microns. This precision is a key factor in their widespread use. From computer rendering to the final packaging, precision turned parts maintain near-perfect forms and shapes throughout the entire production process.
Precision turned parts ensure uniformity in size, shape, and quality thanks to meticulous process control and the use of CAD renderings during production. This consistency guarantees that parts are reliable and minimizes production errors, a rarity with CNC and Swiss screw machining. Additionally, each finished part meets the highest quality standards.
By eliminating defects, rejects, and production errors, the resources used in manufacturing are optimized, resulting in minimal waste. Parts are produced swiftly and efficiently, reducing production time. These benefits lower the cost per part, enhancing profitability and providing a competitive edge.
Modern precision machining ensures parts are crafted swiftly and with high accuracy, leading to faster delivery times that align with client needs. In today’s fast-paced market, quick turnaround is crucial due to competitive pressures and the demands of assembly and manufacturing. This efficiency is particularly advantageous for companies with tight production schedules and strict deadlines.
Precision turning can be used to shape and form virtually any material. The components created through this process exhibit outstanding strength and durability, making them ideal for various sectors such as aerospace, automotive, medical, and electronics—fields that demand the highest levels of precision and accuracy.
Precision-turned components are produced with exceptional quality, resulting in parts that are stronger, more resilient, and capable of enduring greater pressure and stress. This robustness makes them essential for assemblies that must remain dependable and function reliably over extended periods.
As precision-turned parts begin as CAD designs, they can be readily modified and tailored to meet the specific demands of unique or unconventional applications. This flexibility allows for adjustments during production if the requirements for a component evolve due to design or assembly considerations.
The meticulous planning involved in producing precision-turned parts considers the minimization of waste throughout the manufacturing process. The use of computerization plays a key role in reducing waste, as CAD designs are optimized to produce parts efficiently and economically, often eliminating the need for additional processing.
One of the notable advantages of precision-turned parts is their superior finishing. These parts can achieve an excellent surface quality that allows for polishing, treatment, or coating, resulting in a professional and uniform appearance. This high-quality finish not only boosts the value of the parts but also enhances their reliability.
Precision turning can effectively shape a wide range of metals, thanks to the robust cutting and shaping tools that are adapted to the density and hardness of each metal. This technique can accommodate various materials, including steel, bronze, brass, aluminum, copper, and titanium. Additionally, certain types of engineering plastics are also suitable for precision turning, expanding the versatility of the process.
Aluminum's numerous beneficial characteristics make it an excellent choice for producing precision-turned parts. Its machinability allows for the creation of parts with very tight tolerances and intricate designs. Furthermore, aluminum's properties can be improved through plating, which enhances its hardness and conductivity, making it a viable alternative to materials like copper, steel, or stainless steel.
Brass is well-suited for precision-turned parts where high strength is not a critical requirement. Its attractive, bright finish and ease of machining make it a preferred choice for parts with complex and detailed designs. The formability of brass facilitates the creation of intricate components. However, the presence of tin and zinc limits its use in applications involving vacuum environments.
Although copper is more expensive, it is carefully evaluated for use in precision-turned parts due to its valuable properties. Copper's corrosion resistance, excellent conductivity, and non-magnetic nature make it an attractive choice. Like brass, copper offers high formability and is particularly well-suited for electronic components and various hardware applications. Its ability to be easily machined and its compatibility with precision turning further enhance its appeal.
Titanium, initially found as a chemical oxide, is refined into a silver-colored metal known for its low density, high strength, and corrosion resistance. Alloyed with other metals, titanium forms exceptionally strong, lightweight, and durable alloys suitable for diverse applications, from aerospace to jewelry and sports equipment. Its biocompatibility has also made it a preferred material in medical procedures. Titanium's impressive strength-to-weight ratio makes it particularly advantageous for precision-turned parts where both strength and reduced weight are crucial.
Steel, encompassing both stainless and carbon varieties, has long been a staple in the production of precision-turned parts due to its strength, durability, and ease of machining. The characteristics of steel can differ based on its alloying elements, which define its grade. The specific alloys added influence the steel's suitability for various applications and the types of precision-turned components it can effectively produce.
Screw machined parts are complex pieces that are typically cylindrical and threaded and a screw machined product is a family of automatic lathes for small to medium-sized components...
Thread rolling is a type of threading process which involves deforming a metal stock by rolling it through dies. This process forms external threads along the surface of the metal stock...
The normal functioning of CNC machines is done along the three Z, X, and Y axes. The five axes machines have two more axes accessible, which are namely A and B. The addition of the two extra axes makes it easy to cut complex and intricate parts...
CNC machining is an electromechanical process that manipulates tools around three to five axes, with high precision and accuracy, cutting away excess material to produce parts and components. The initial designs to be machined by CNC machining are created in CAD...
The CNC process was developed in the 1950‘s and took a leap forward in the 1980‘s with the addition of computerization. Unlike other production processes, CNC begins with a rendering by a computer, which creates a two or three dimensional representation of the part to be produced...
Contract manufacturing is a business model in which a company hires a contract manufacturer to produce its products or components of its products. It is a strategic action widely adopted by companies to save extensive resources and...
EDM machining is a contemporary machining method based on the removal of material from a part using thermal energy. The material is removed by local melting or vaporizing small areas on the surface of the part being machined...
G-code is the name of a plain text language that is used to guide and direct CNC machines. For most modern CNC machines, it isn‘t necessary to know the meaning of G-codes since CAD and CAM software is translated into G or M codes to instruct a CNC machine on how to complete a process...
Computer numerical control (CNC) is a fundamental part of modern manufacturing. The majority of machines operate using instructions and guidelines that have been downloaded using a CNC program controller...
Sinker Electrical Discharge Machining (EDM) is a metal machining process used to create molds, dies, and parts using electrical sparks to erode material from a workpiece. It is preferred over other machining processes due to...
A method of precision machining called electrical discharge machining (EDM) removes material from a workpiece using thermal energy rather than mechanical force. A thin, single-strand metal wire and deionized water used to...
Machining is a manufacturing process used to produce products, parts, and designs by removing layers from a workpiece. There are several types of machining that include the use of a power driven set of machining tools to chip, cut, and grind to alter a workpiece to meet specific requirements...
The CNC process, computer numerical control, is a method of manufacturing where programmed software directs the operation of factory tools and machinery. It is designed to manage a wide range of complex machines from grinders and lathes to mills and routers...